The Importance of Quality in Nickel Alloys Materials Suppliers
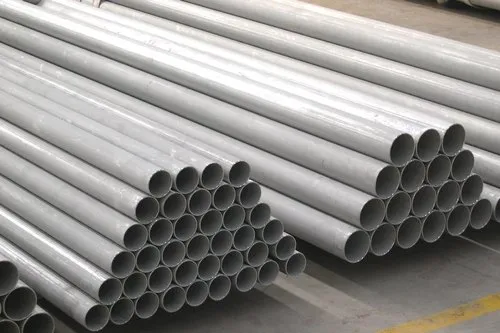
Nickel alloys are essential materials used in various industries due to their exceptional properties such as high corrosion resistance, excellent mechanical strength, and ability to withstand extreme temperatures. These attributes make them indispensable Inconel 625 Strip in sectors like aerospace, power generation, chemical processing, and marine engineering. However, the performance and reliability of nickel alloy components are highly dependent on the quality of the materials supplied. This essay explores the importance of quality in nickel alloys materials suppliers, highlighting the critical role they play in ensuring the efficiency, safety, and longevity of industrial applications.
Ensuring Material Integrity and Performance
The quality of nickel alloys directly impacts the integrity and performance of the components manufactured from them. High-quality nickel alloys exhibit consistent chemical compositions and superior metallurgical properties, which are crucial for achieving the desired mechanical strength and corrosion resistance. Suppliers that maintain stringent quality control measures ensure that their products meet industry standards and specifications, providing engineers and manufacturers with reliable materials that perform as expected under demanding conditions. Conversely, low-quality alloys with impurities or inconsistencies can lead to premature failures, costly downtimes, Hastelloy C-276 Alloy Strip and safety hazards.
Enhancing Safety and Reliability
In industries where safety is paramount, such as aerospace and power generation, the reliability of nickel alloy components is critical. Quality suppliers adhere to rigorous testing and certification processes to verify the performance of their materials under various operating conditions. This includes tests for tensile strength, fatigue resistance, creep resistance, and corrosion resistance. By providing certified and traceable materials, suppliers help ensure that the final products can withstand extreme environments and stresses, reducing the risk of catastrophic failures. For instance, in the aerospace industry, where components are subjected to high pressures and temperatures, the use of high-quality nickel alloys is vital for maintaining the safety and reliability of aircraft engines and other critical parts.
Meeting Industry Standards and Regulations
The production and application of nickel alloys are governed by stringent industry standards and regulations to ensure the safety and performance of components. Quality suppliers are well-versed in these standards, such as ASTM (American Society for Testing and Materials) and ISO (International Organization for Standardization), and ensure their materials comply with the specified requirements. Compliance with these standards is essential for manufacturers to obtain certifications for their products and gain the trust of their clients. Reliable suppliers also keep abreast of any changes in regulations and adapt their processes accordingly, providing manufacturers with up-to-date materials that meet the latest industry standards.
Supporting Innovation and Advanced Applications
The continuous development of advanced applications in various industries drives the need for innovative nickel alloy materials with enhanced properties. Quality suppliers invest in research and development to create new alloys and improve existing ones, enabling manufacturers to push the boundaries of what is possible. For example, in the power generation industry, the development of nickel-based superalloys with superior high-temperature strength has allowed for more efficient and durable turbine blades, contributing to increased energy efficiency and reduced emissions. By partnering with quality suppliers, manufacturers can leverage cutting-edge materials to innovate and stay competitive in their respective fields.
Cost Efficiency and Long-Term Benefits
While high-quality nickel alloys may come at a premium, they offer significant long-term benefits and cost efficiencies. Components made from superior materials tend to have longer service lives, reducing the need for frequent replacements and maintenance. This not only lowers operational costs but also minimizes production downtimes, enhancing overall productivity. Moreover, quality suppliers often provide comprehensive technical support and after-sales services, helping manufacturers optimize the use of their materials and resolve any issues promptly. The initial investment in high-quality materials is thus offset by the long-term savings and improved performance of the final products.
Conclusion
The importance of quality in nickel alloys materials suppliers cannot be overstated. From ensuring material integrity and performance to enhancing safety, reliability, and compliance with industry standards, quality suppliers play a pivotal role in the success of various industrial applications. They support innovation and advanced applications by providing cutting-edge materials and offer long-term cost efficiencies through durable and reliable products. Manufacturers and engineers must prioritize working with reputable suppliers to achieve optimal results and maintain the high standards required in their industries. The commitment to quality in nickel alloys not only drives technological advancements but also ensures the safety, efficiency, and sustainability of critical infrastructure and systems.