Understanding the Different Types of CNC Machining Tools
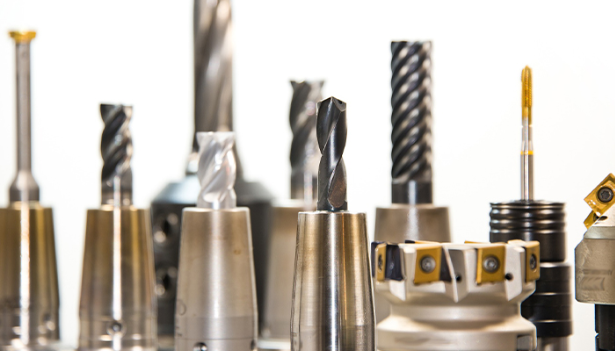
CNC machining has transformed modern manufacturing by providing unparalleled precision, efficiency, and repeatability. At the heart of CNC machining are the tools that shape, cut, and refine raw materials into finished parts. These tools come in various types, each designed for specific machining operations, such as milling, turning, drilling, and grinding.
Understanding the different types of CNC machining tools is crucial for optimizing production processes, improving product quality, and reducing operational costs. In this guide, we’ll explore the most common CNC machining tools, their functions, and how they contribute to the overall manufacturing process. This article will provide valuable insights into the essential tools that power precision manufacturing.
Common Types of CNC Machining Tools
CNC machining tools come in various shapes and functions, each designed for specific operations like cutting, shaping, drilling, and finishing. Below, we’ll explore some of the most common CNC machining tools and their applications in modern manufacturing.
Turning Tools
They are primarily used in CNC lathes to remove material from a rotating workpiece. These tools perform operations such as facing, threading, grooving, and boring to create cylindrical parts with high accuracy. Single-point cutting tools are the most common in turning, where a fixed tool removes layers of material as the workpiece spins. Depending on the application, different tool geometries and coatings are used to enhance tool life and performance. High-speed steel (HSS) and carbide inserts are popular choices, offering durability and precision for machining metals, plastics, and composites.
Milling Tools
These tools use rotating cutters to remove material from a stationary workpiece. These tools come in various shapes, including end mills, face mills, and ball nose mills, each suited for specific tasks. End mills, for example, are ideal for contouring, slotting, and profiling, while face mills provide a smooth finish on large surfaces. Milling tools are often made from carbide or cobalt steel to withstand high cutting forces and temperatures. Advanced coatings like titanium nitride (TiN) further improve wear resistance, making them suitable for machining tough materials like stainless steel and titanium.
Drilling Tools
Machinists use these tools to create precise holes in a workpiece, a crucial step in many manufacturing processes. CNC drilling machines rely on drill bits of various sizes and geometries to achieve different hole diameters and depths. Twist drills are the most common type, featuring spiral flutes that help remove chips and improve cutting efficiency. Other specialized drill bits, such as center drills, spot drills, and step drills, allow for precise hole positioning and finishing. Modern CNC drilling operations often integrate coolant-through drill bits to reduce heat buildup and prolong tool life, ensuring consistent hole quality in high-speed machining environments.
Grinding Tools
Grinding tools are used in CNC grinding machines to achieve high-precision surface finishes and tight tolerances. These tools consist of abrasive wheels that remove material by grinding it down at a microscopic level. Grinding is commonly used for finishing hardened metals, sharpening tools, and refining components that require extreme accuracy. Cylindrical grinders, surface grinders, and centerless grinders each serve specific functions, allowing manufacturers to achieve smooth, defect-free surfaces. Advanced grinding wheels made from diamond or cubic boron nitride (CBN) offer superior durability and cutting performance, making them ideal for hard metals and superalloys.
Cutting Tools
They play a fundamental role in CNC machining, enabling the precise removal of material to achieve the desired shape and dimensions. These tools include various types of saws, such as band saws and circular saws, used for cutting metal sheets, bars, and tubes. Plasma cutters and laser cutters provide non-contact cutting solutions for high-speed, intricate designs. CNC cutting tools are designed to maximize efficiency while minimizing waste, ensuring that each cut is accurate and clean. The choice of cutting tool depends on the material being processed, with carbide-tipped blades and diamond-coated cutters offering enhanced longevity and precision.
Tapping Tools
Manufacturers also use tapping tools for creating internal threads in a workpiece, allowing screws and bolts to be securely fastened. CNC tapping machines use high-speed rotating taps to cut precise threads in metals, plastics, and composites. There are different types of taps, including straight-flute taps for through holes and spiral-flute taps for blind holes. Some metal CNC machines use rigid tapping, where the spindle and tap move in perfect synchronization, ensuring uniform thread depth and accuracy. Advanced coatings such as titanium carbonitride (TiCN) increase wear resistance and prolong tool life, making tapping tools more efficient for high-volume production.
Choosing the Right Tool for Your Application
The choice of a CNC machining tool depends on several factors, including the material being machined, the type of operation, and the desired surface finish. Using an inappropriate tool can lead to poor-quality parts, excessive tool wear, and increased production costs. Here are key considerations for your project.
Matching Tools to Materials
Different materials require specific tools to achieve optimal cutting performance and longevity. Softer materials like aluminum and plastic can be machined with high-speed steel (HSS) tools, which offer good cutting efficiency at lower costs. However, harder materials like stainless steel, titanium, and hardened alloys demand carbide or cubic boron nitride (CBN) tools due to their superior wear resistance and heat tolerance. Additionally, tool coatings such as titanium nitride (TiN) or aluminum titanium nitride (AlTiN) improve tool life and performance by reducing friction and preventing heat buildup.
Tool Selection for Specific Tasks
Each machining operation requires a tool designed for the specific task at hand. Milling operations, for example, benefit from end mills, face mills, or ball nose cutters, depending on whether contouring, finishing, or slotting is required. Turning applications rely on specialized cutting inserts for facing, threading, and grooving. Drilling operations require different types of drill bits, including twist drills, step drills, and carbide drills, depending on hole depth and diameter.
Balancing Speed, Feed Rate, and Tool Life
Optimizing cutting speed and feed rate is essential for prolonging tool life while maintaining machining efficiency. Running a tool at excessive speeds can cause overheating, premature wear, and even tool failure, while operating too slowly may lead to poor surface finish and inefficient machining cycles. Manufacturers use cutting data from tool manufacturers and real-time monitoring systems to determine the ideal speed and feed rate for each material and tool combination. Adjusting these parameters based on the workpiece material, tool geometry, and coolant application ensures maximum productivity while minimizing downtime and tooling costs.
Considering Tool Coatings and Treatments
Tool coatings and surface treatments play a significant role in enhancing tool performance and durability. Titanium nitride (TiN) is a widely used coating that reduces friction and extends tool life, making it suitable for general-purpose machining. Aluminum titanium nitride (AlTiN) provides superior heat resistance and is ideal for machining hardened steels. Diamond coatings are used for cutting non-ferrous materials like graphite and composites, ensuring extended tool longevity. Surface treatments such as cryogenic treatment and nitriding further enhance wear resistance, improving tool performance in high-stress machining environments.
Importance of Tool Holders and Stability
Tool performance isn’t just about the cutting edge; the stability of the tool holder also plays a critical role. A secure and vibration-free tool holder ensures precise cuts and extends tool life by preventing excessive wear and chatter. Collet chucks, hydraulic chucks, and shrink-fit holders are commonly used to provide rigid and precise clamping of cutting tools. Poor tool holding can lead to runout, uneven cuts, and reduced surface finish quality.
Cost Efficiency in Tool Selection
While high-performance tools may have a higher upfront cost, they often result in long-term savings by reducing tool replacements and improving machining efficiency. Low-cost tools may seem budget-friendly, but frequent tool changes, reduced cutting speeds, and poor surface finishes can drive up production costs. Evaluating factors such as tool longevity, machining time, and part quality helps manufacturers strike a balance between cost and performance. In many cases, investing in premium tools with advanced coatings and optimized geometries results in higher productivity and better-quality components. So, they are a more cost-effective choice in the long run.
Adapting to New Technologies in CNC Tooling
Advancements in CNC tooling technology are constantly improving machining capabilities, offering smarter and more efficient solutions. Modern developments include indexable cutting tools, which allow for quick insert changes without replacing the entire tool, reducing downtime. High-performance solid carbide tools with specialized geometries improve material removal rates while maintaining precision. Additionally, adaptive machining technologies and real-time tool monitoring systems help optimize tool wear, improving efficiency and reducing unexpected failures.
Conclusion
From turning and milling tools to drilling and grinding solutions, each tool plays a crucial role in shaping high-quality components. Remember to match tools to materials, optimize cutting parameters, and leverage advanced coatings and technologies. This way, you can enhance productivity and reduce downtime. Also, stay informed about the latest tooling innovations. This will help your business remain competitive and achieve superior machining results.